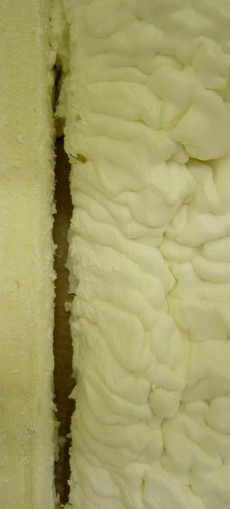
Last week we talked about Troubleshooting SPF and learned about off-ratio foam. This week we are going to discuss another type of poor quality spray foam that needs attention, shrinking foam and voiding foam.
If you recall these posts, Processing, Part II, Processing Open Cell Foam, Processing Closed Cell Foam(feel free to review them if you have not seen them already), you may remember that the SPF reaction is temperature sensitive and that we discussed a “window of application”, referring to the acceptable processing temperature range to make good quality foam. Well, when foam is applied outside of this window of application, either higher or lower, a few different things can happen that result in sub-standard spray foam quality.
If the processing temperatures are too high, you can see shrinkage; where after the foam fully expands, it pulls away from the side(s) of the cavity, and you will likely see a crack between the foam and the stud that was not there after the spray pass was completed.
This occurs because the speed of the reaction was too fast. As the blowing agent leaves the cell it creates a negative pressure inside the atom and the atom collapses resulting in a loss of yield. In this situation, the high heat has caused the speed of the plastic formation reaction to go to fast, causing instability; the proper corrective action is to lower the heat. When you experience shrinkage you can start by lowering the hose heat a few degrees at a time while trying to dial in the proper temperature. After a few attempts of lowering the hose heat, if shrinkage is still present, it may be necessary to lower the temperature settings on the primary heaters; I recommend making these adjustments in 2-3 degree increments.
The opposite effect of shrinkage is voids, or hollow air pockets created between the foam and the substrate or inside the foam itself, caused when the chemicals are too cold or when a cold substrate absorbs too much heat from the chemicals. This causes the plastic formation reaction to slow down and lag, resulting in large cell structure and blowing agent release on the backside of the foam, which separates the foam from the substrate leading to voids behind, or inside, the expanded foam. The reaction temperature needs to be hotter, to speed up the reaction, so proper corrective actions include: increasing the substrate temperate, increasing the chemical temperatures and possibly moving the spray gun closer to the substrate, especially when the ambient air is very cold, by moving the gun closer to the substrate the atomized chemical will have less dwell time in the ambient air and will get to the wall at a higher temperature, increasing the reaction temperature on the wall.
With this guidance on how to handle shrinkage and voids, your teams will be better prepared to manage obstacles in the field, when they occur. Best of luck and stay tuned next week as we discuss jobsite cleanup.
Subscribe here to get your FREE copy of 25 Spray Foam Insulation Frequently Asked Questions from Spray Foam Advisor.