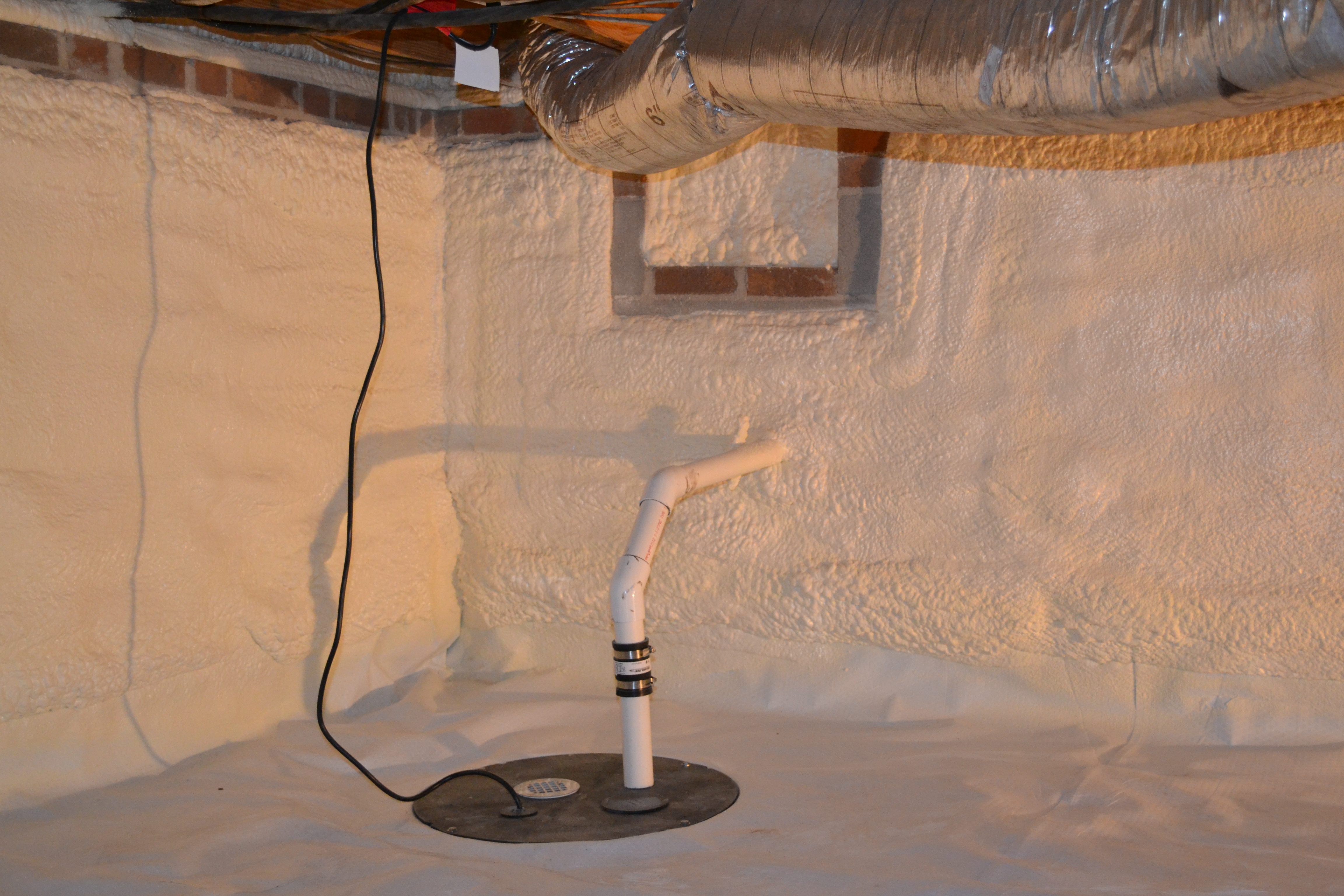
Last week, in Air Exchange in Closed Attics, we discussed the idea of air exchange in closed attics that use open cell foam.
This week we are going to move to another part of the building envelope and talk about unvented crawl spaces.
This application is often lumped in with attics, most likely because the IRC code section for foam plastics, IRC 316, has the same limitations and requirements for attics and crawl spaces, and these locations are generally not considered occupied or living spaces of the building.
Regardless, as you have read over the last few weeks in Both Vented and Unvented Attics Work, Conditioned Attics Change Heat Load Calcs and Air Exchange in Closed Attics, they can be designed to operate in various ways. Even though these areas are not typical living spaces if attics and crawl spaces are designed and constructed poorly, the building and its occupants could pay the price.
Traditional crawl spaces often experience issues with moisture & bulk water and can be a key area associated with building air leakage and the stack effect.
By creating unvented crawl spaces, you can significantly improve moisture control, reduce air leakage and get the additional benefit of energy savings.
When it comes to unvented crawl spaces, one of the best resources for information is www.crawlspaces.org, a compilation of data from closed crawl space research conducted by Advanced Energy.
Here are a few closed crawl space reference documents that Advanced Energy has created:
Quick Reference on Crawl Spaces
Design, Construction and Performance for Crawl Spaces
Advanced Energy identifies six major categories related to good crawl space design, these include:
- Moisture Management
- Pest Control
- Combustion Safety
- Fire Safety
- Thermal Insulation
- Radon Control
Moisture Management – Includes proper drainage, air sealing and a fully sealed vapor retarder are critical for good design.
Pest Control – Includes termite inspection band at the top of the perimeter wall should be included in the design.
Combustion Safety – Requirements vary based on the present components but should include direct-vent combustion appliances, carbon monoxide monitors or alarms for buildings with an attached garage or combustion appliances and raw-gas leak alarm if fuel-fired appliances or fuel lines are present.
Fire Safety – Includes air sealing of sub-floor and proper documentation to allow installation of exposed materials.
Thermal Insulation – Insulation can be applied to the sub-floor, on the interior perimeter wall surface, on the exterior perimeter wall surface or inside the perimeter wall, and should be installed without gaps or compression and in full contact with the insulated surface (sub-floor or perimeter wall). If the perimeter wall is insulated, a non-porous insulation, like closed cell foam, should be used.
Radon Control – US EPA recommends testing all homes for radon. In areas where radon is a risk, buildings with closed crawl spaces can be mitigated with sealing and venting techniques.
This is the beginning of how to approach unvented or closed crawl spaces. Stay tuned next week as we look at the code section for closed crawl spaces and one process for approaching a closed crawl space using closed cell foam.
Subscribe here to keep in touch with Spray Foam Advisor and get your FREE copy of 25 SPF Frequently Asked Questions and a PRIVATE link to Robert Naini’s SPFA Breakout Session, “3 Ways to Close More Sales with Building Science.”